Our last blog post focused on a comprehensive approach to Troubleshooting Pumps and Process Equipment in the Field. Here, we offer specific troubleshooting tips for four of the most common pump failures that we encounter in our day to day work of servicing pumps, working with pumps, and manufacturing pump packages and chemical metering systems.
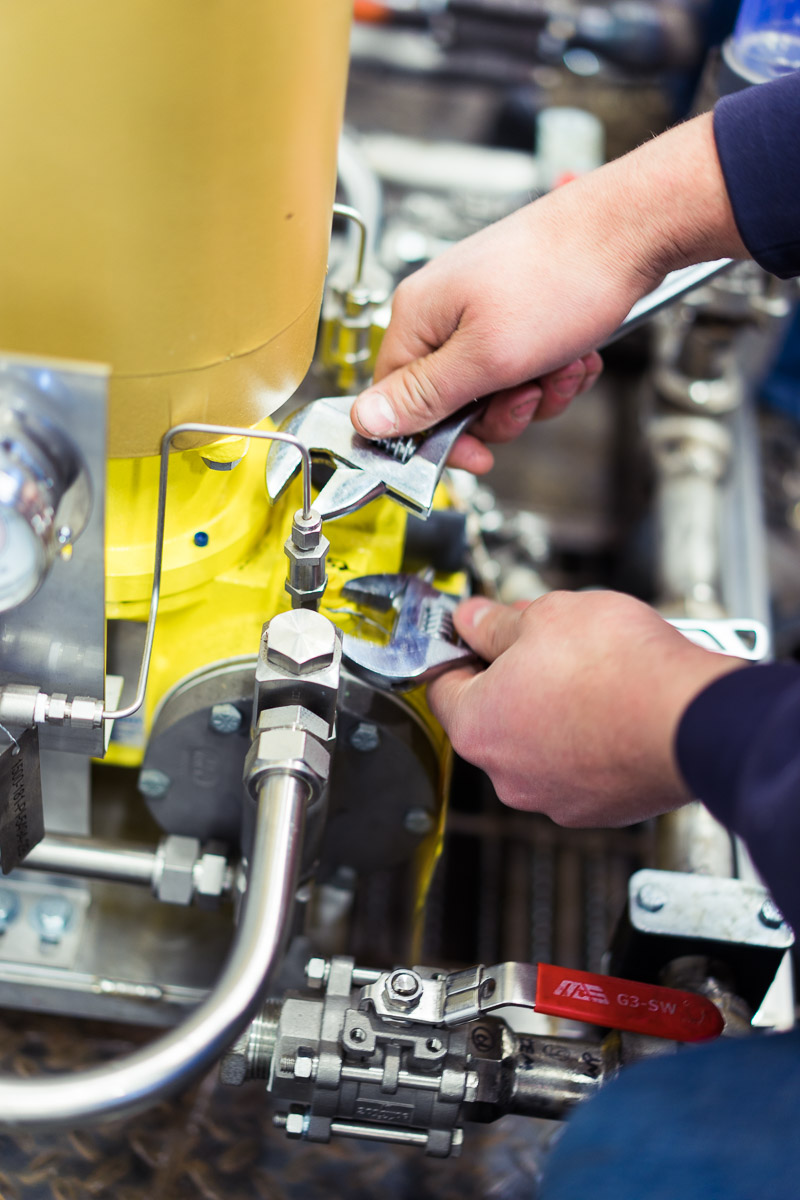
Pump problem #1: No Flow
No chemical is being drawn down from the calibration column. No fluid is detected at the pump package discharge point.
Is the pressure gauge moving (indicating pressure with each stroke)?
- If the answer is NO, check for loss of prime, faulty check valves, starving suction, internal mechanical damage.
- If the answer is YES, check for blocked discharge, relieving through the internal PRV or external PSV.
Pump problem #2: Reduced Flow
The flow coming from the pump is reduced.
Possible causes:
- Failing check valves:
- Old chemical residue. Perhaps the valves are not sealing properly and require cleaning.
- Damage or scoring. This would prevent the ball and/or the seat from sealing properly.
- Starved suction or cavitation on suction:
- Check for blocked valves or blockages in lines.
- Check the supply tank, it may be empty.
- Pump is air locked/insufficient prime:
- If this is the case, you need to prime/bleed air from the pump by opening the pump discharge to the atmosphere while operating, until fluid is observed. Caution! Wear proper safety equipment to protect against being splashed with chemical. Bleed chemical into a safe area or container.
- Insufficient Revolutions Per Minute (RPM) at the motor or rotation direction at the motor:
- The inverter may not be set to output the correct RPM or direction. Locate the arrow for indication of correct rotation on the pump or consult the pump manual if a specific rotation is required.
- Excessive discharge pressure:
- The discharge line could be partially restricted causing a buildup of pressure above the internal pressure relief valve in the pump. This can create an internal bypass and prevent the pump from displacing the full chemical volume.
- Check to see if the pressure gauge is reaching the same pressure as the internal pressure relief in the pump.
- Increase the pump’s internal pressure relief setting if it is safe to do so. Caution! First determine if all components on the pump package, discharge line and at the injection point can handle the higher pressure.
- Wrong chemical viscosity:
- Too low for creating a proper seal in a gear type pump or too high (causing cavitation) for the size of pump or package lines and components. Select a more suitable pump or increase the suction line and/or components.
- Partial blockage of the pump or discharge lines: check if the pressure gauge is indicating higher than usual pressure. If it is, you are creating more back pressure than usual somewhere along the discharge line between the pump outlet and the injection point or quill. Isolate the location by safely opening the line at various points and testing the flow rate. Caution! Wear Protective Equipment and de-pressurize the lines before opening any connections.
- Increased pressure at the injection point or process line: The process line you are injecting into may have increased in pressure and therefore the pump has reduced capacity against this higher pressure.
- Pump seal is leaking: Look for signs of chemical leakage externally from the pump or within the oil reservoir. Improperly sealing check, piston, or diaphragm seals may be drawing in air during the suction stroke. Look for very small amounts of leakage around the seals.
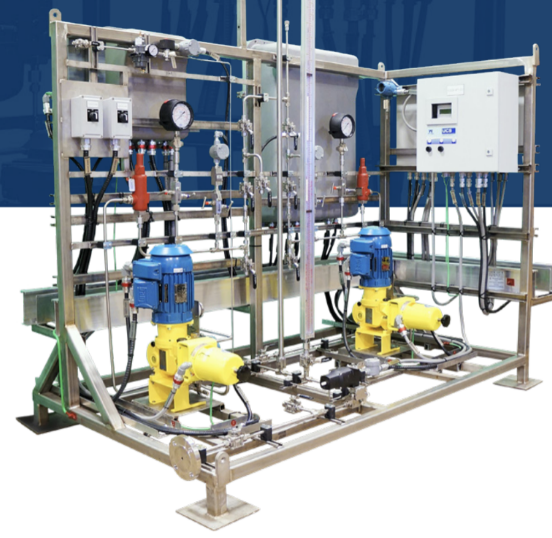
Pump problem #3: Pump is not running after turning on the power.
Possible causes:
- No power at the motor – this could indicate a blown fuse, a tripped breaker or a damaged or bad connection/cable to the motor.
- Damaged or seized motor.
- Damaged or seized pump.
- Wrong voltage motor or wrong voltage supplied to the motor.
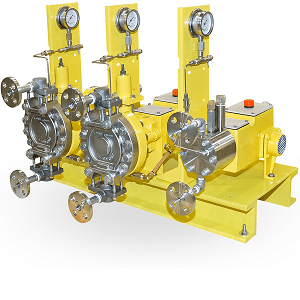
Pump problem #4: Pump keeps losing prime or becomes air locked.
Possible causes:
- Air is trapped in the head of the pump:
- Certain chemicals, particularly popular ones like Sodium Hypochlorite (bleach), peracetic acid and hydrogen peroxide create gas and higher vapour pressures especially when they become contaminated and decompose. This air from this off-gassing becomes trapped in the head of the pump. The pump compresses and decompresses the air without moving it out of the head until enough air builds up to completely displace the fluid and prevent flow.
- When handling these chemicals be sure to have filters or appropriate piping/handling procedures to prevent organics from entering the tank/lines which will create faster decomposition of the chemicals. Some of these chemicals will create high/unsafe temperatures due to exothermic reactions. Light and heat can create quicker decomposition.
- To prevent slow moving chemical that has more time to release gas, minimize the diameter of the supply lines between the tank and the pump to only the size required and no larger. If the problem persists, you may also require an open column on the suction line vented to a safe area or ideally back to the tank to help remove the excess gas.
- Air trapped in the system: due to insufficient priming or leaks in the suction line.
- A high point in the suction line: causing an air trap or an air pocket on the line.
We hope these tips for troubleshooting common pump failures will help guide you to the root of your issue, or at least provide you with a starting point for solving your pump problem. Start by reviewing the general steps for Troubleshooting Pumps and Process Equipment in the Field, and be systematic in your approach. If, after following these troubleshooting tips, you have not been successful in solving the pump problem, it may be time to call in an expert. Wave Control’s trained service technicians can assist with the repair and servicing of pumps, chemical injection packages, electrical equipment, industrial equipment, and various control systems.